The efficient and safe conveyance of fluids and gasses is critical in industrial settings for various activities. Process pipework is crucial in this aspect, as it provides a network of interconnected pipes that facilitate the flow of materials within industrial systems. This blog will look at the importance of process piping, its components, and its critical role in ensuring the smooth running of industrial facilities.
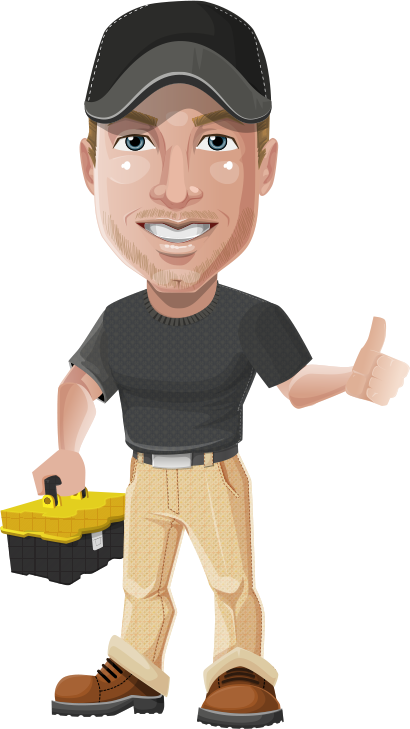
Definition and Purpose
A system of pipes used to transfer fluids, gasses, and other materials throughout industrial processes is referred to as process pipework. Its principal function is to ensure the efficient operation of various industrial systems by facilitating the transfer of chemicals from one area to another. Manufacturing, oil and gas, chemical plants, pharmaceuticals, and power generation industries use process piping.
Components of Process Piping
Process pipework comprises several components that work together to build an extensive network. These elements are as follows:
Pipes
The pipes themselves are the system’s backbone. They are available in various materials, sizes, and combinations depending on the purpose. Steel, stainless steel, copper, and plastic are commonly used to process pipes.
Fittings
Fittings join pipes and redirect fluid flow. Elbows, tees, couplings, unions, and valves are examples of fittings. Fittings provide a secure and leak-free connection between pipes and the ability to alter and change the direction of the piping system.
Flanges
Flanges connect pipes and provide a leak-tight seal. They are frequently affixed to the terminals of pipes, making assembly and disassembly simple. Flanges are commonly employed in systems that necessitate routine maintenance or component replacement.
Pipe Supports and Hangers
Pipe supports and hangers are used to secure and suspend pipes in their appropriate positions. These parts ensure the lines are correctly aligned, supported, and shielded from undue stress or strain.
Gaskets
Gaskets seal flanged connections and prevent leakage. They are typically constructed of rubber, cork, or metal.
Design and Construction
Process piping design and fabrication necessitate careful planning and adherence to industry standards. Engineers and designers evaluate the system’s requirements, considering pressure, temperature, material compatibility, and flow rates. They create detailed designs and drawings describing the layout, pipe sizing, and component specs.
Process pipeline fabrication entails cutting, bending, and welding pipes to generate the appropriate designs. Pipefitters and welders use their expertise to assure exact assembly, leak-free connections, and structural integrity. Quality control techniques are applied throughout fabrication to ensure compliance with applicable regulations and standards.
Installation and Maintenance
Process piping installation requires skilled professionals who are well-versed in industrial systems. We meticulously install the piping system, considering alignment, support, and accessibility for maintenance and repairs. Rigorous testing ensures the integrity and functionality of the installed system.
To ensure continued performance, regular maintenance is essential. Our team conducts inspections, repairs, and replacements as necessary. Regularly checking for leaks, corrosion, and structural issues prevents potential problems and maintains the system’s efficiency and safety.
Final Thoughts
Countless plumbers and engineers are at your disposal if you need a process piping system put in, maintained, or fixed. At Scott’s Plumbing, we are equipped to handle any process pipe system in any industry. We can assist businesses in all major industrial sectors, including the textile, petroleum, paper, and pharmaceutical industries. Our plumbers prioritize safety, adhere to industry standards, and guarantee that process piping systems work optimally. Call us now!